Intensive Mixer is a high-speed agitation mixer developed by Maschinenfabrik Gustav Eirich (Germany) based on its unique mixing principle and know-how accumulated over many years.
The mixer is composed of a rotating mixing pan (mixing vessel), a rotor tool (mixing tool) positioned eccentrically to the center of the mixing pan, and Tool set (bottom/wall scraper) designed to prevent build-up of material on the wall and bottom of the mixing pan. The mixing pan rotates clockwise, while the mixing tool rotates counterclockwise (or clockwise) at high speed, creating a strong shear force onto the materials to be processed.
In addition, multiple processes such as mixing, granulating/pelletizing, kneading, and slurrying can be handled in a single machine by adjusting operating conditions.
A wide range of lineup is available, from 1L/batch up to 8,000L/batch for Type-R (mixing pan inclined type) and up to 12,000L for Type-D (mixing pan horizontal type). The most suitable machine type will be selected according to your requirements.
Our products are used in many industries that require raw material processing, including industrial chemicals, construction materials, ceramics, and glass etc.
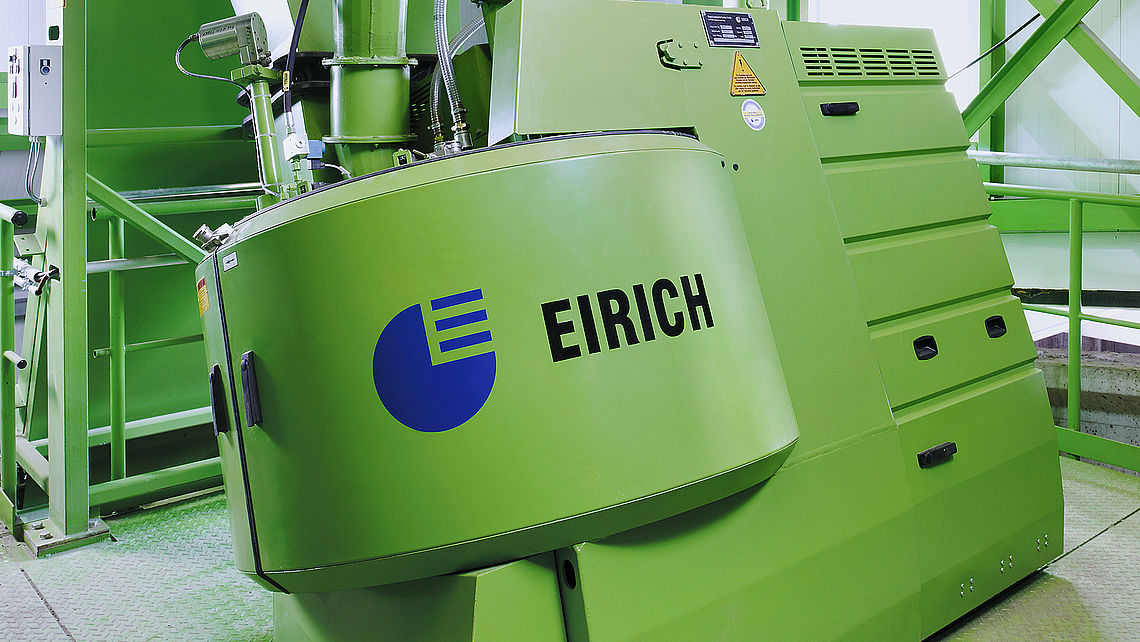
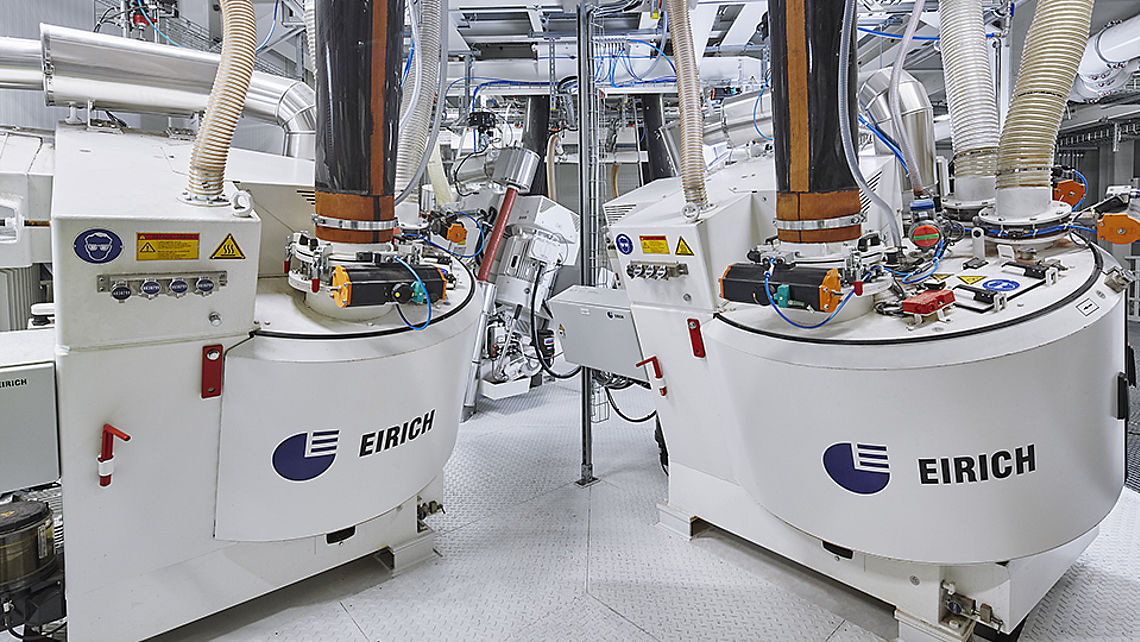
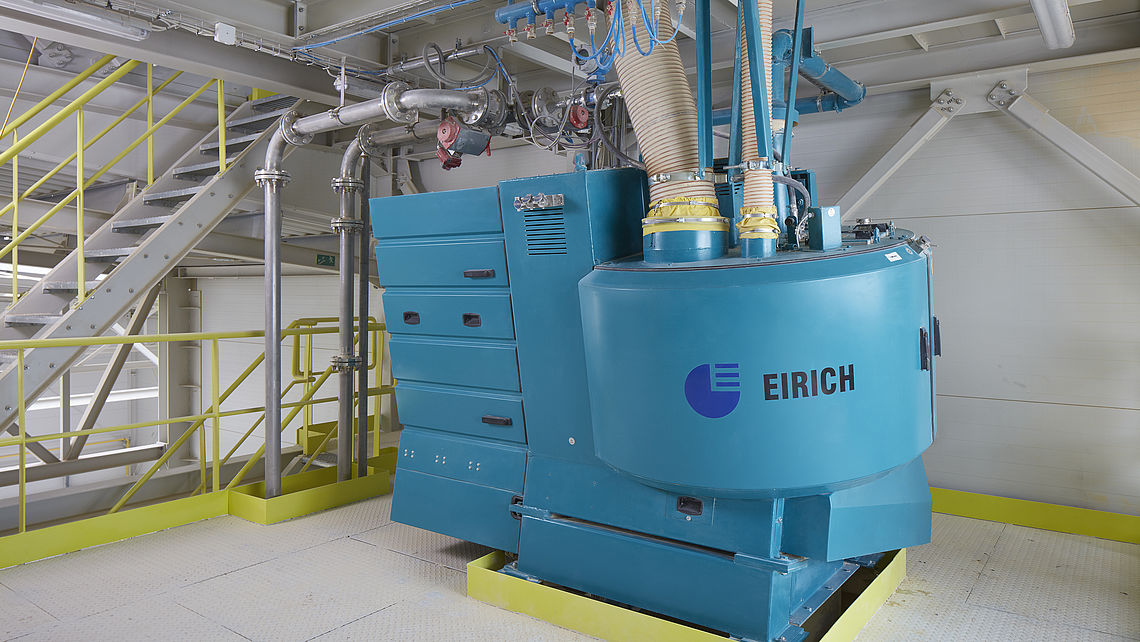
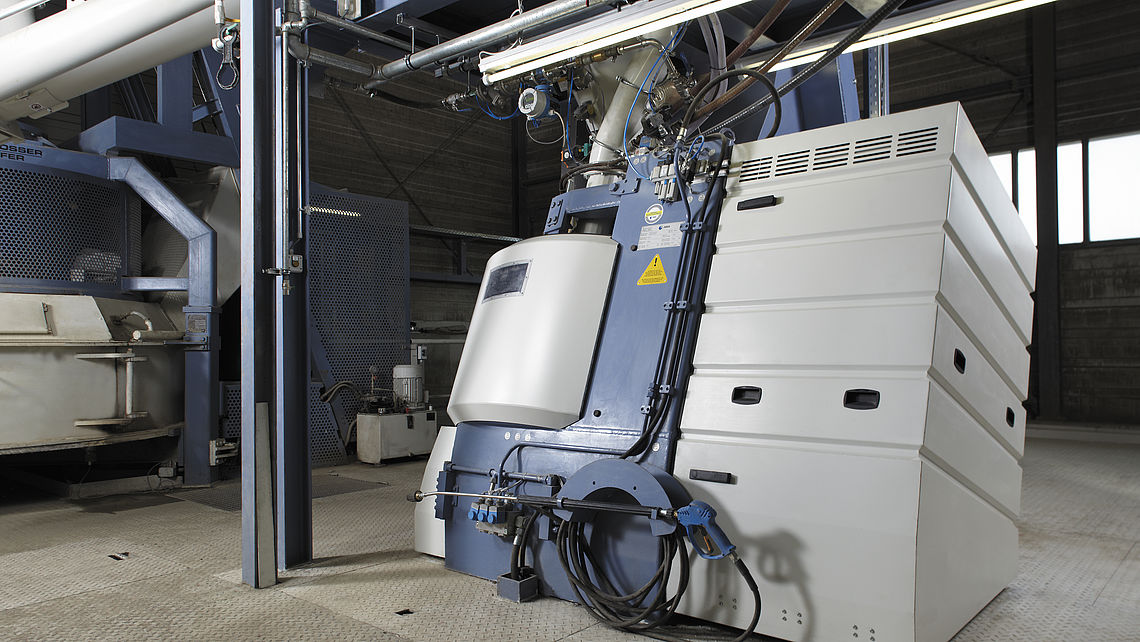
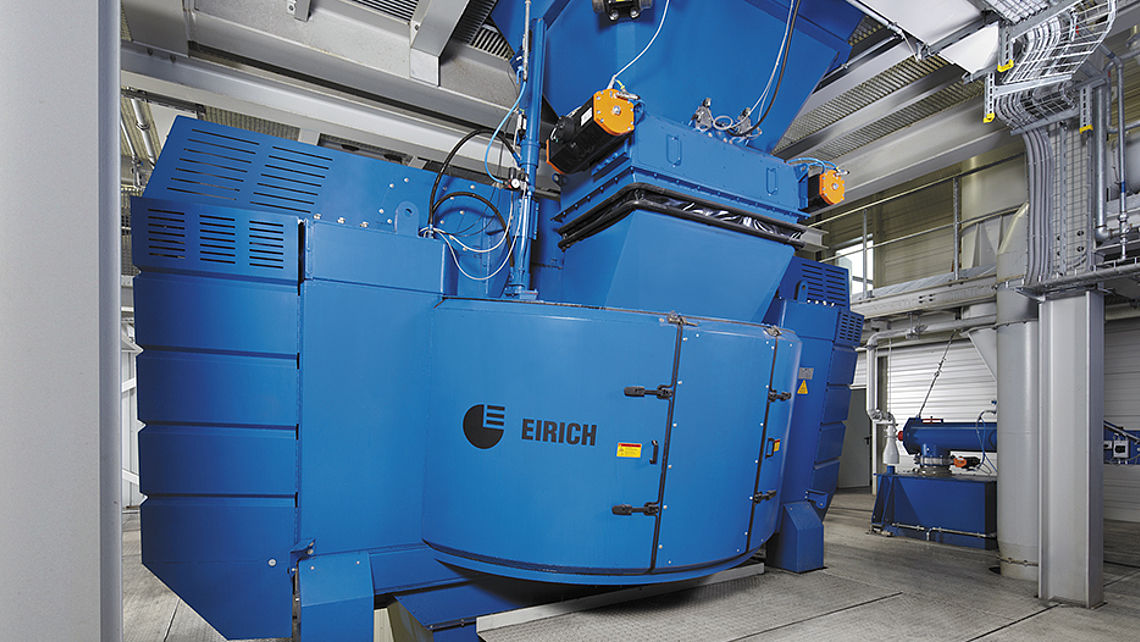
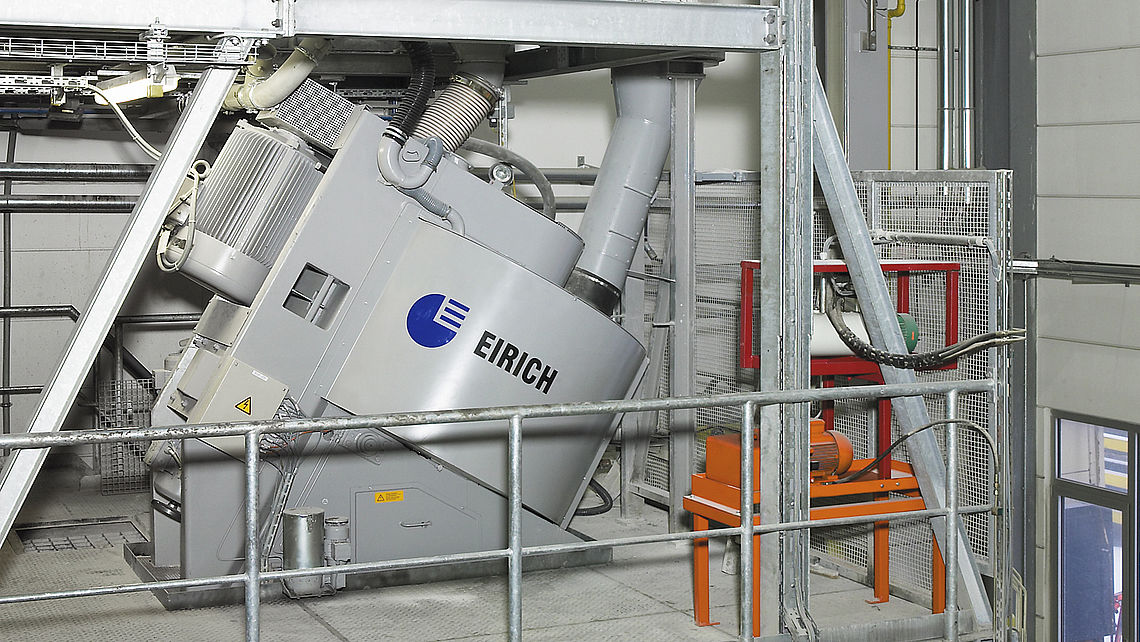
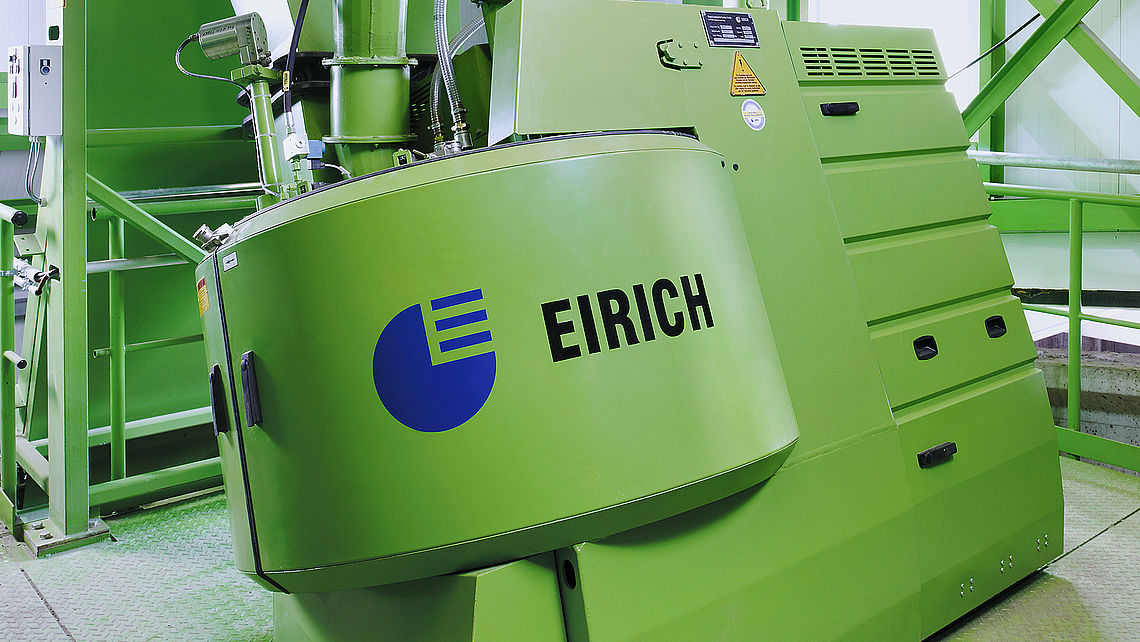
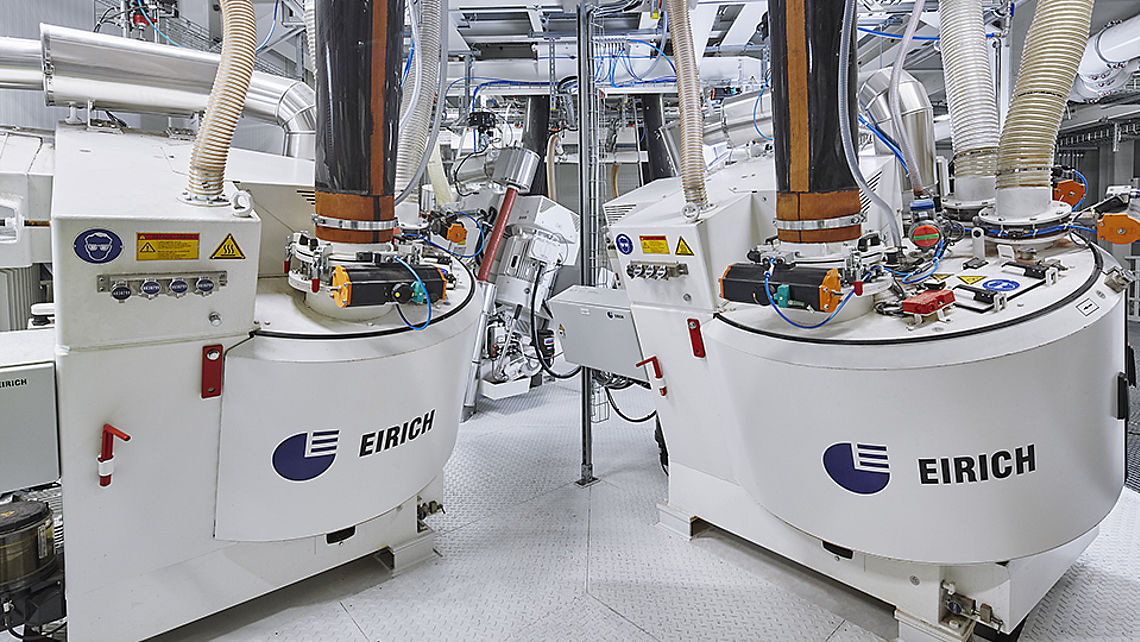
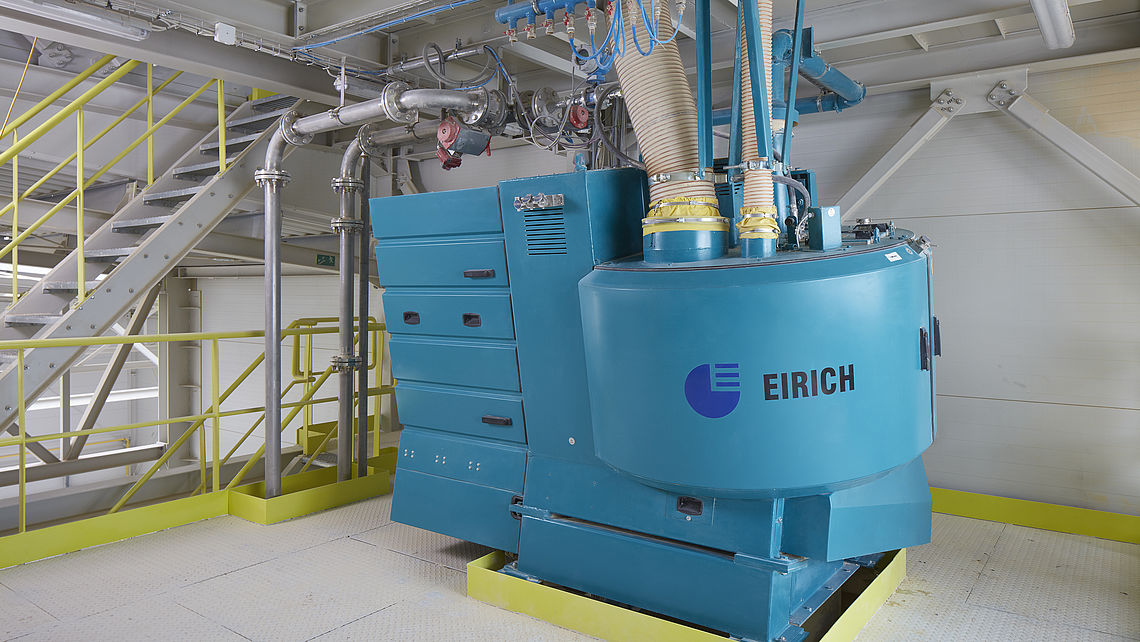
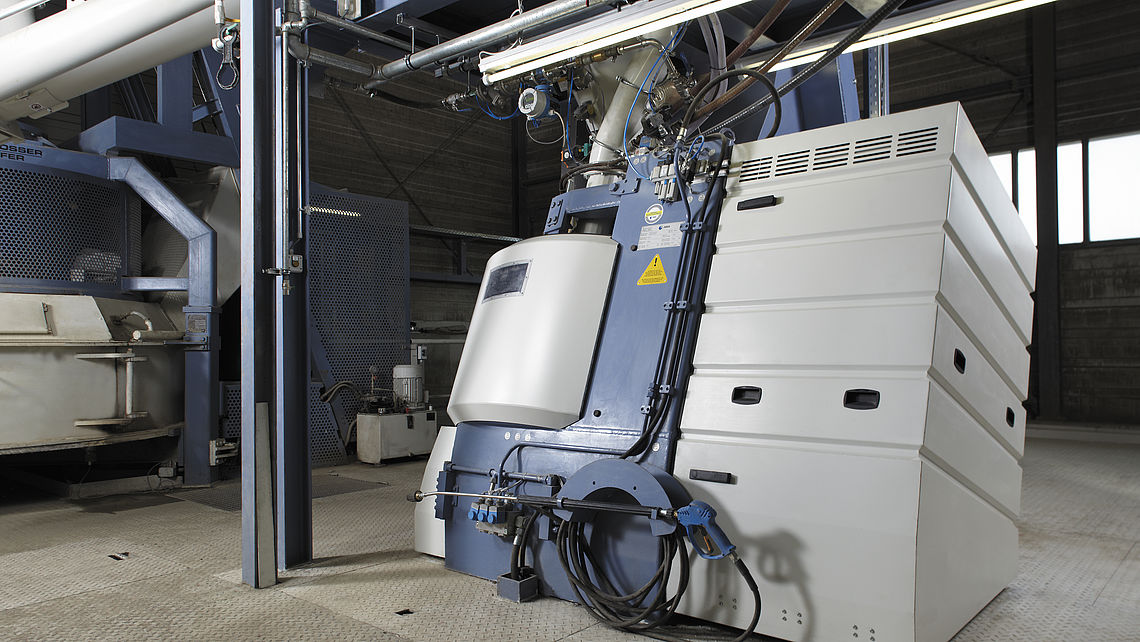
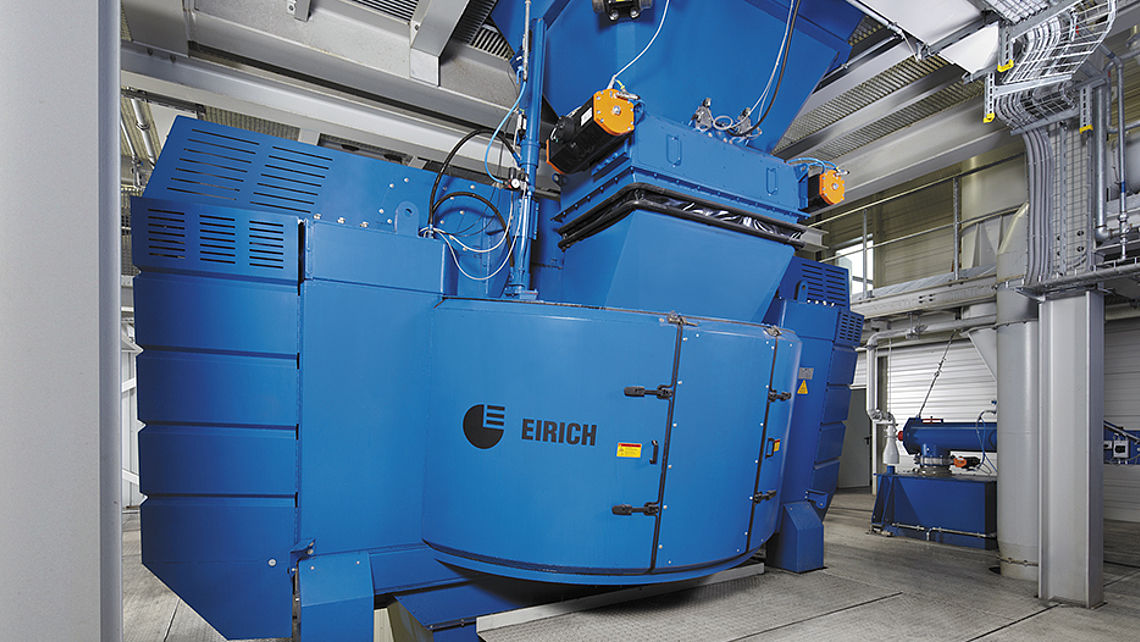
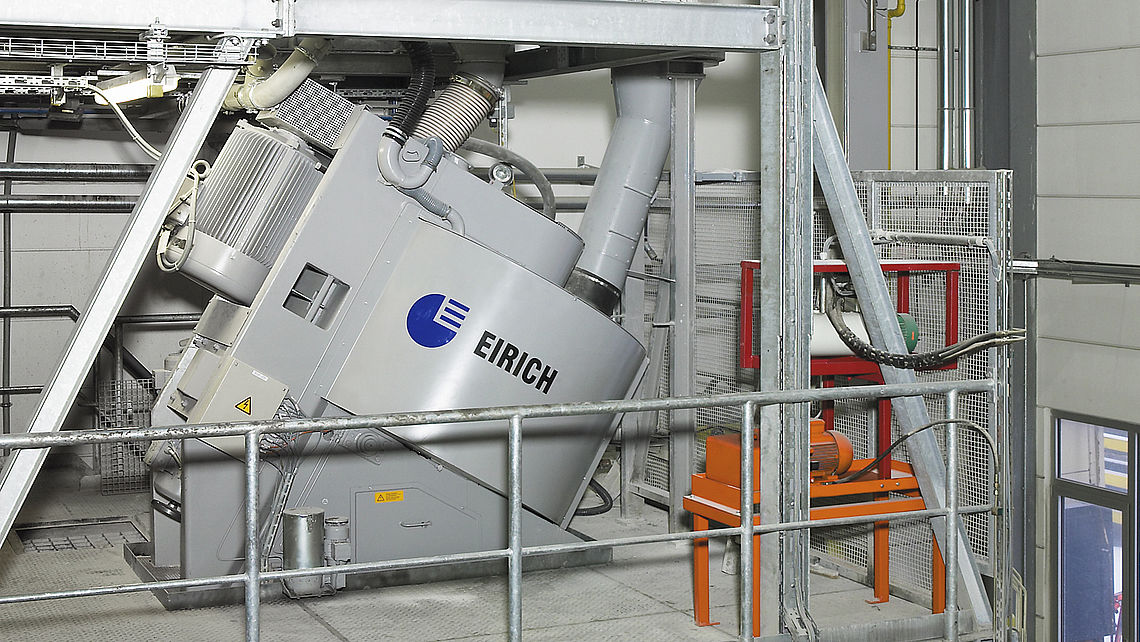
Major processes
- Optimized homogenization of the process material, and excellent, stable quality of the mixed product in the shortest mixing time, thanks to the unique Eirich mixing principle
- High operating rate with minimal maintenance, thanks to a simple and robust structure
- For various purposes regardless of viscosity properties of raw materials
- A full lineup from lab machines (min. 1L/batch) to large machines (max. 12,000L/batch)
- Able to simplify existing process
- Continuous and batched operating modes

Three core components of Eirich Intensive Mixer are: an eccentrically positioned rotor tool (mixing tool), tool set (bottom/wall scraper), and the rotating mixing pan (mixing vessel).
1. Rotor tool (mixing tool)
Rotor tool is positioned eccentrically to the center of the mixing pan, enabling efficient shear force onto the material. The speed can be set according to the purpose of processing, from high speed for high shear force to low speed for gentle agitation. The design and direction of rotation can also be selected according to the process requirements. A bottom tool attached to the bottom end of the rotor tool prevents build-up of material on the bottom of the mixing pan.
2. Tool set (bottom/wall scraper)
Tool set prevents build-up of material on the wall and bottom of the mixing pan. It also changes the direction of material flow and promotes the homogenization of the process material inside the mixer.
3. Mixing pan (mixing vessel)
The rotating mixing pan moves the mix into the path of the mixing tool.
Mixers Type R
Capacity | Mode of Operation | Operating Mode | Country of Origin | |||||
---|---|---|---|---|---|---|---|---|
Type | liters | Kg max. | Batch | Continuous | Standard Atmospheric pressure |
Under Vacuum |
Japan | Germany |
EL1/EL1-INOX | 1 | 1.6 | ● | ● | ● | |||
EL5 Eco(R02) | 3 - 5 | 8 | ● | ● | ● | ● | ||
EL5 Profi | 3 - 5 | 8 | ● | ● | ● | |||
EL5 Profi Plus | 3 - 5 | 8 | ● | ● | ● | |||
EL10 Profi | 8 - 10 | 12 | ● | ● | ● | |||
EL10 Profi Plus | 8 - 10 | 12 | ● | ● | ● | |||
R02 VAC | 3 - 5 | 8 | ● | ● | ● | ● | ||
R05T | 15 - 40 | 65 | ● | ● | ● | ● | ||
RL05T | 15 - 40 | 65 | ● | ● | ● | ● | ||
R08 | 75 | 120 | ● | ● | ● | ● | ||
R08W | 75 | 120 | ● | ● | ● | ● | ||
R08 VAC | 75 | 120 | ● | ● | ● | ● | ||
R09 | 150 | 240 | ● | ● | ● | |||
R09W | 150 | 240 | ● | ● | ● | ● | ||
R09T | 150 | 240 | ● | ● | ● | ● | ||
R11 VAC | 250 | 400 | ● | ● | ● | ● | ||
RV11 VAC | 375 | 600 | ● | ● | ● | ● | ||
R12 | 250 | 400 | ● | ● | ● | ● | ||
RV12 | 400/500 | 800 | ● | ● | ● | ● | ||
R12W | 250 | 400 | ● | ● | ● | |||
RV12W | 400/500 | 650 | ● | ● | ● | ● | ||
RLV12W | 400/500 | 650 | ● | ● | ● | |||
RLV12W VAC | 400/500 | 650 | ● | ● | ● | ● | ||
R15 VAC | 500 | 800 | ● | ● | ● | ● | ||
RV15 VAC | 750 | 1,200 | ● | ● | ● | ● | ||
R16 | 600 | 960 | ● | ● | ● | ● | ● | |
RV16 | 900 | 1,440 | ● | ● | ● | ● | ● | |
R16W | 600 | 960 | ● | ● | ● | |||
RV16W | 900 | 1,440 | ● | ● | ● | |||
RLV16 | 900 | 1,440 | ● | ● | ● | |||
R19 | 1,125 | 1,800 | ● | ● | ● | ● | ● | |
RV19 | 1,500 | 2,400 | ● | ● | ● | ● | ● | |
RV23 VAC | 3,000 | 4,800 | ● | ● | ● | ● | ||
R24 | 2,250 | 3,600 | ● | ● | ● | ● | ● | |
RV24 | 3,000 | 4,800 | ● | ● | ● | ● | ● | |
RLV24 | 3,000 | 4,800 | ● | ● | ● | |||
R28 | 4,000 - 5,500 | 6,400 - 8,800 | ● | ● | ● | ● | ||
R32 VAC | 5,250 | 8,400 | ● | ● | ● | ● | ||
RV32 VAC | 7,000 | 11,200 | ● | ● | ● | ● | ||
R33 | 6,000 - 8,000 | 9,600 - 12,800 | ● | ● | ● | ● |
Note: Mixer types beginning with RL are for slurry applications.
Mixers Type D
Capacity | Mode of Operation | Operating Mode | Country of Origin | |||||
---|---|---|---|---|---|---|---|---|
Type | liters | Kg max. | Batch | Continuous | Standard Atmospheric pressure |
Under Vacuum |
Japan | Germany |
DE22 | 1,500 | 2,400 | ● | ● | ● | |||
DEV22 | 2,250 | 3,600 | ● | ● | ● | ● | ||
DWL22 | 2,250 | 3,600 | ● | ● | ● | |||
D23 | 1,500~3,000 | 2,400~4,800 | ● | ● | ● | |||
DEV29 | 4,000 | 6,400 | ● | ● | ● | |||
DW29/3 | 3,000 | 4,800 | ● | ● | ● | |||
DW29/4 | 4,000 | 6,400 | ● | ● | ● | |||
DW29/5 | 5,000 | 8,000 | ● | ● | ● | |||
DWL29/5 | 5,000 | 8,000 | ● | ● | ● | |||
DWL29/6 | 6,000 | 9,600 | ● | ● | ● | |||
DW29/6 | 6,000 | 9,600 | ● | ● | ● | |||
DW31/7 | 7,000 | 11,200 | ● | ● | ● | |||
DW40 | 12,000 | 19,200 | ● | ● | ● |
Note: Mixer types beginning with DWL are for slurry applications.
EIRICH Smart Discharger (ESD), Suction-type Product Discharge Device
This is a suction-type product discharge device that uses a combination of a nozzle attached to the top of the mixing pan and a vacuum generator.
The pneumatic discharge mechanism allows discharge without damaging products and requires no operator intervention until product discharge is complete. The product can be discharged to any destination, such as to a product storage container or to the next process.
Advantages
- Discharge without damaging products, thanks to a pneumatic discharge mechanism
- Complete material discharge because the rotation of the mixing pan promotes product discharge
- Significant reduction of dust emission during discharge, because of no need to open and close the mixer until discharge is complete
- Work in a closed environment from the start of operation to the completion of discharge, possible
- Reduction of transportation process to the next process, labor saving, and shortening of the process, possible
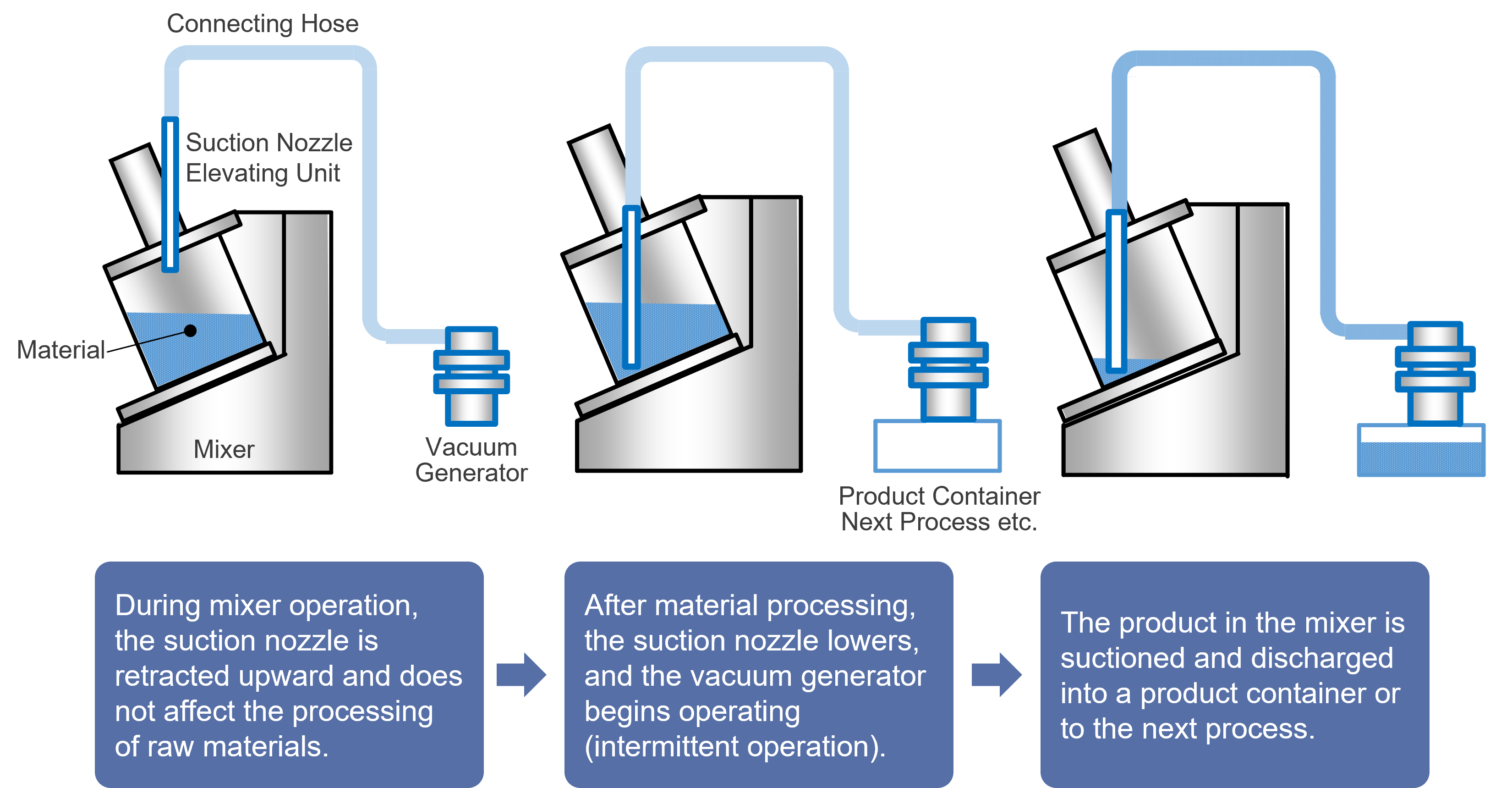
Key milestones in the development of a wide variety of industries and applications are firmly linked to Eirich mixing technology. The entire process can be performed in a normal atmosphere and in a vacuum. More
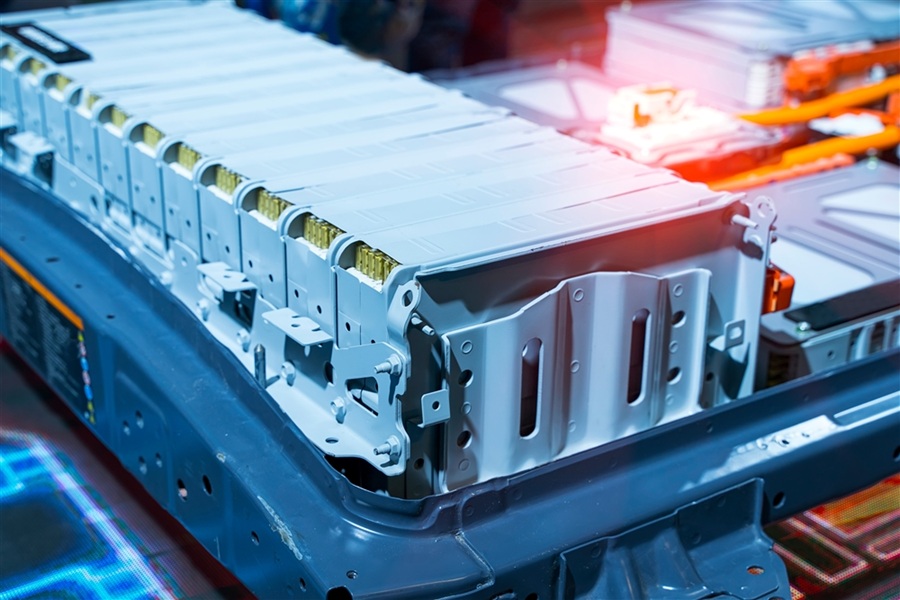
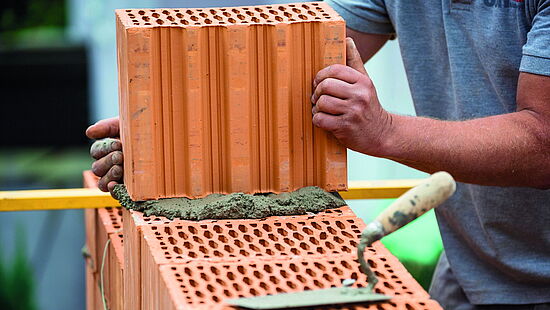
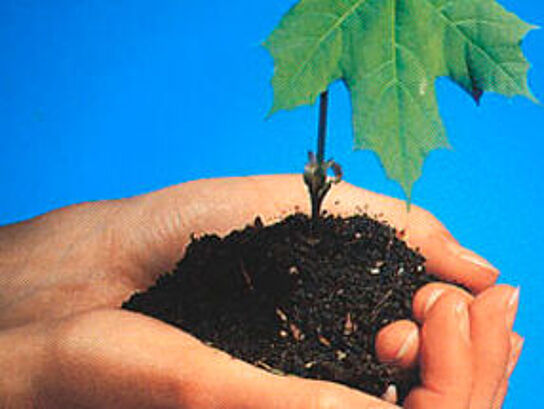
Industrial Chemicals
Cogeneration batteries, secondary batteries, lithium-ion batteries, capacitors, fuel cells, friction linings
Building Materials
Siding, roofing materials, interlocking block, concrete, dry mortar, stucco
Environmental Protection
Incinerator ash, coal ash, iron and steel dust, industrial sludge, contaminated soil
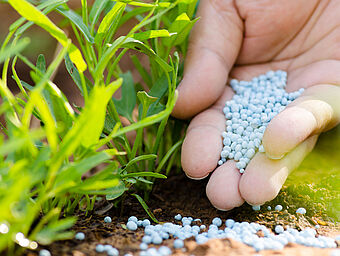
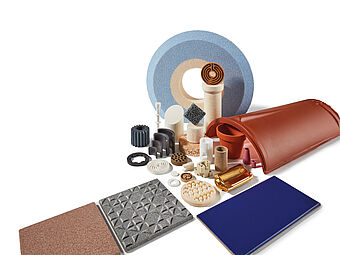
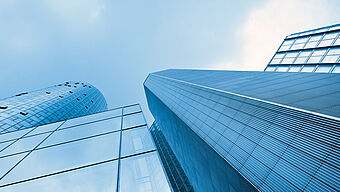
Agricultural Chemistry
Fertilizers, feed, pesticides, and soil
Ceramics
Tiles, refractories, graphite products, electronic components, catalysts
Glass
FPD glass, sheet glass
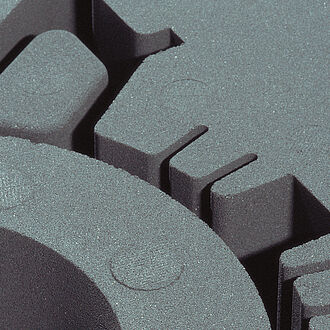
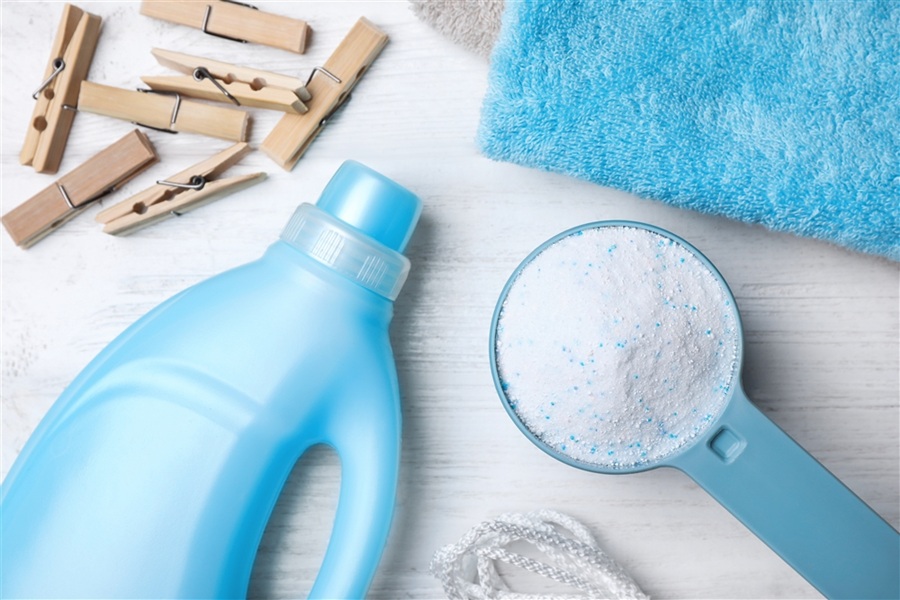
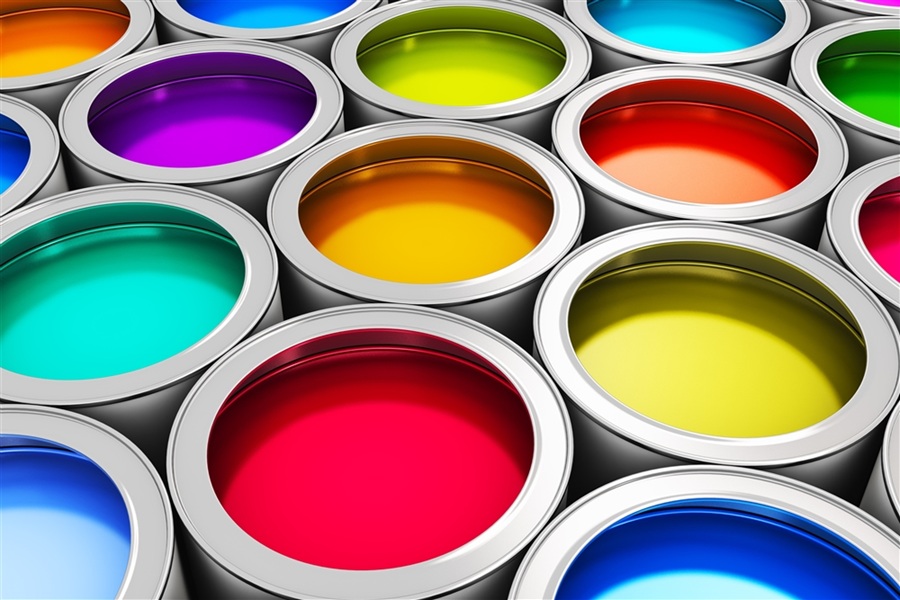
Green Sand
Molding sand
Chemical Products
Chemical raw materials, silicone, detergents, soap
Paint/Ink/Coating
Color resists, pigments, inks, paints, coating materials
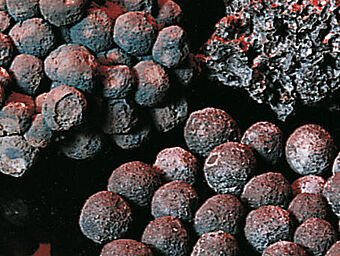
Metallurgy
Iron ore, non-ferrous metal ore, welding raw materials
(pdf, 3 MB)
EIRICH Intensive Mixer
(pdf, 427 KB)
EIRICH Laboratory Mixer Type EL1
Raw Material Processing Examples
We proposes more ideal material processing by combining the know-how accumulated by Eirich Group around the world with our own technological development efforts.